PRODUCTS CENTER —— 产品展示 —— |
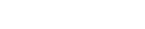
24-hour hotline
18002573585 |
|
|
On-line detection technology of safety valve with linear displacement sensor
Safety valve is an overpressure protection device applied to pressure-bearing equipment in electric power, petroleum and chemical industries, which is mainly used for pipelines and various pressure-bearing equipment. When the working pressure of medium exceeds the allowable pressure value, the safety valve will automatically open to discharge medium, and with the decrease of medium pressure, the safety valve will be closed again, thus preventing the overpressure danger of pipelines and equipment and ensuring the safe operation of the system. At present, the safety valve calibration technology mainly includes off-line calibration and on-line calibration.
Off-line calibration of calibration bench means that the safety valve is installed on the calibration bench, then the safety valve is opened by using calibration medium, and the opening pressure is confirmed by observing the pressure gauge. This method can not consider the calibration of back pressure safety valve and safety valve of high temperature or low temperature medium; On-line instrument calibration is to measure the downward spring force acting on the safety valve by external force, so as to calculate the opening pressure of the safety valve. On-line instrument calibration generally does not affect production, and the detection speed is relatively fast, but this method cannot detect the sealing performance of the safety valve.
At present, the identification techniques of valve flap micro-opening applied to safety valve online calibration system mainly include probe method, audio frequency method, displacement method, inflection point identification method of additional external force curve and so on. The probe method uses special mechanical devices to place probes when the applied force reaches a certain level. When the valve stem moves and the valve disc opens, the probe disconnection identification method is used to identify the movement of the valve stem and the opening of the valve disc. Because it is easily affected by the deformation of the mechanical clamp, the moment when the probe is disconnected cannot effectively represent the slight opening of the valve flap. Therefore, the disadvantage of this method is the large measurement error.
Audio method is mainly used in the detection of safety valve in hot state. When the valve flap is opened, air flow sound will be detected by the pickup probe and identified by audio amplification. The disadvantage of this method is that human factors have great influence on the measurement accuracy. At the same time, the safety valve must work in hot state, which limits its application effect.
Displacement method is to detect the displacement of the valve stem in real time by a displacement sensor. When the displacement reaches a certain value, the valve stem is considered to be open. Because the mechanical device is easy to deform under the action of additional force, and the deformation is affected by the external force. For different pressure valves, the additional force is different when opening, so the deformation of mechanical clamp is different. Therefore, it is difficult to use fixed displacement to judge the valve opening state, otherwise it will bring measurement error.
The inflection point identification method of additional external force curve is an improvement of displacement method. Spring deformation stress curve method mainly uses spring deformation stress curve to identify valve micro-opening. Micro-opening of the disc will cause displacement of the valve stem, which can be detected by the displacement sensor. Combined with the relevant theoretical basis of the inflection point identification method of the additional force curve, when detecting the additional force, the displacement change of the displacement sensor is used as the trigger signal to start measuring the additional force. The slope of spring deformation stress curve before slightly lifting the valve flap is obviously higher than that after slightly lifting the valve flap. The advantage of spring deformation force curve method is that the displacement produced by the displacement sensor is used as the trigger signal to start the measurement of the pressure sensor, so it is unnecessary to apply additional force evenly, and the micro-opening recognition of the valve flap is accurate.
The peripheral structure of online calibration system includes mechanical clamp and hydraulic jack. Among them, the mechanical clamp provides a stable and reliable force application environment for additional external force, and ensures that the safety valve can work normally during online measurement. The hydraulic jack is responsible for outputting high-pressure hydraulic power, which is converted into upward driving additional force which can act on the valve clack, so as to open the safety valve clack. The displacement sensor is fixed on the valve stem through a mounting bracket, and the measuring rod can be adsorbed on the fixture base through a magnet. When the valve stem moves upward under the action of additional force, the displacement sensor can detect the displacement of the valve stem. The pressure sensor is limited on the valve stem, and the valve stem passes through the hydraulic jack, the stress plate of the pressure sensor and the central round hole of the mechanical clamp base, and the hydraulic jack is fixed on the stress brackets on both sides of the mechanical clamp. Under the joint action of the limit nut and the fixed bracket, the hydraulic jack can provide a force application environment with additional force acting on the valve stem through the pressure sensor. At the same time, the additional force exerted by the hydraulic jack can be detected by the pressure sensor. The data acquisition system collects the output signals of the displacement sensor and the pressure sensor in real time, and obtains the additional external force value acting on the valve stem at the moment of micro-opening of the valve flap in combination with the data analysis system, so that the company can calculate and obtain the opening pressure value of the safety valve and realize the online calibration of the safety valve.
|